Making Use of the Advantages of Ultrashort Pulse Lasers in Laser Cutting
Glass is indispensable for the modern consumer industry. The transparent material is used mainly for displays on smartphones, tablets, and screens. The demands on glass processing have also increased considerably because of the constant further development and large-scale production of these products. The laser is the tool of choice for cutting thin display glass sheets quickly, precisely, economically, and in the required quantities. However, the characteristic properties of glass are also a challenge for the laser: Glass is brittle, transparent to visible light, has low thermal conductivity and, if heated unevenly, tends to produce stress that can lead to cracks.
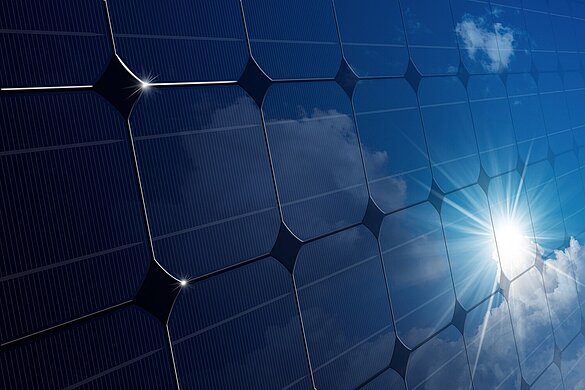
So-called ultrashort pulse (USP) lasers can overcome these challenges. The laser pulses in the picosecond and femtosecond range allow strong localization of the energy input and also change the absorption mechanism of transparent materials due to the high photon density. The laser beam focuses on individual points inside the glass and modifies the material along the desired separation line. This change in material allows the glass to crack in a controlled way. USP lasers with high throughput can produce smooth, post-processing-free edges - not only on glass, but also on materials such as sapphire, acrylic, diamond, or ceramic. And the potential is far from exhausted.
Due to its low heat input, micrometer-scale processing accuracy and repeatability, USP technology provides new efficient manufacturing solutions for many industrial applications: For example, for structuring polymer and metal alloys or joining different materials, cutting stents from biopolymers, removing thin anti-reflective and passivation layers from solar cells, or drilling microvias on printed circuit boards.
PI supports laser machine builders, laser system integrators, USP laser manufacturers as well as contract manufacturers worldwide with motion, control and software solutions for precision and dynamic positioning of workpieces, lasers, and laser scanners. For example, through CAD/CAM software including laser and galvo scanner operations, or pre-configured multi-axis systems for simple and fast installation and commissioning. This enables us to help our customers to exploit the potential of USP laser technology and to develop advanced machining processes or product features.